3D Printed Stretchable Liquid Gallium Battery
Guilherme Costa
Pedro Alhais Lopes
Afsaneh L. Sanati
André F. Silva
Marta Calisto Freitas
Anibal T. de Almeida
Mahmoud Tavakoli
Despite the rapid progress on soft and stretchable batteries, current fabrication techniques involve manual disposition and stencil/screen printing. Here, for the first time, a 3D-printed Ag–Ga battery is introduced through subsequent printing of four sinter-free composites: a stretchable Liquid Metal (LM) EGaIn-Ag-Styrene-isoprene block copolymers (SIS), and Carbon-SIS current collectors; Ag2O-SIS cathode; and a novel Ga-C-SIS anode. Being sinter-free results in faster printing, and compatibility with heat-sensitive substrates. Although the Ga-C-SIS is solid-like and nonsmearing after printing, it creates a liquid interface after contacting with the electrolyte. This results in a self-feeding and self-aggregation mechanism that brings more gallium to the surface and delays the formation of the dead surface. The recordbreaking areal capacity of ≈19.4 mAh cm−2, along with excellent stretchability (>130% Max. strain), makes the Ag–Ga battery an excellent alternative to Ag–Zn batteries. Surprisingly, digital printing results in 3x higher areal capacity compared to stencil printing, due to greater gallium exposure at the surface. The desired voltage and current output can be customized by printing several battery cells and interconnect them in series/parallel. Also, printing of sensors, electrodes, batteries, and interconnects on a biomonitoring e-textile for simultaneous monitoring of electrocardiography, body temperature, and respiration is demonstrated.
A) Preparation of the gallium-carbon-SIS digitally printable ink: i,ii) First CB is mixed with the SIS solution with the help of Toluene; iii,iv) Melted gallium 60°C is added, and mixed with the solution iv) Ga-C-SIS printable paste. B) When discharging the battery, gallium is converted to gallium (III) oxide whereas the silver oxide turns into metallic silver. The electrons flow from the anode to the cathode. C) Digitally printing a silver– gallium battery: i,vi) Extrusion printer depositing the materials ii,v) Printing the 1st CC. iii,vi) Printing the 2nd CC. iv) Printing the electrodes; vii) Placing the electrolyte. D) The role of carbon in the anode: i) Sheet resistance measurements of gallium electrodes with different CB:Ga ratio; ii) Schematic demonstrating the role of the CB in percolating the gallium particles. E) Digitally printing 2 batteries with 6 cells each in parallel and in series. Each battery had 3 battery cells in parallel and 2 in series.
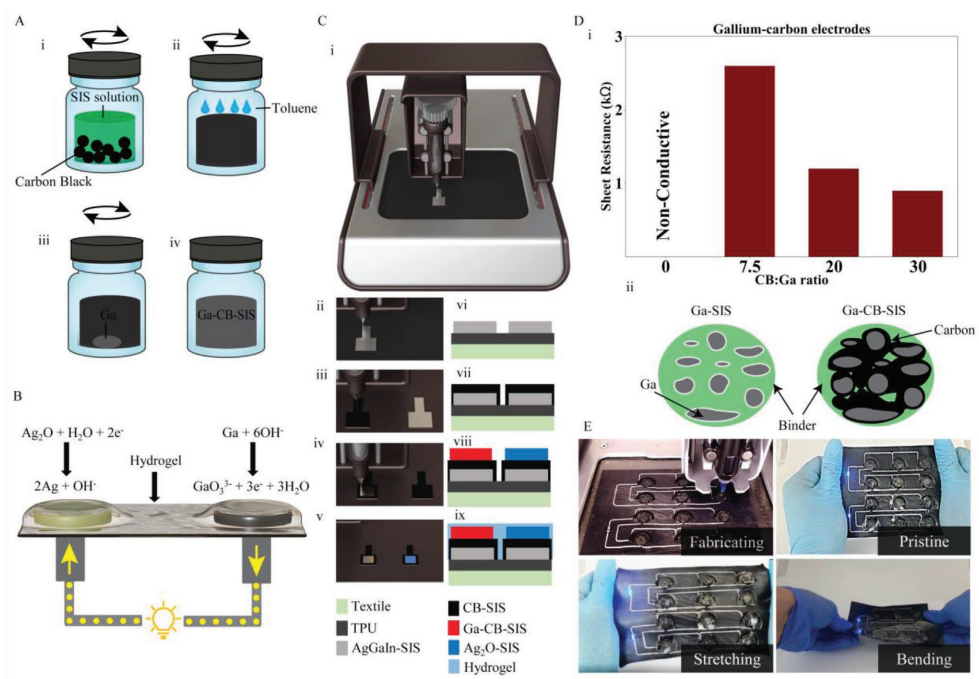
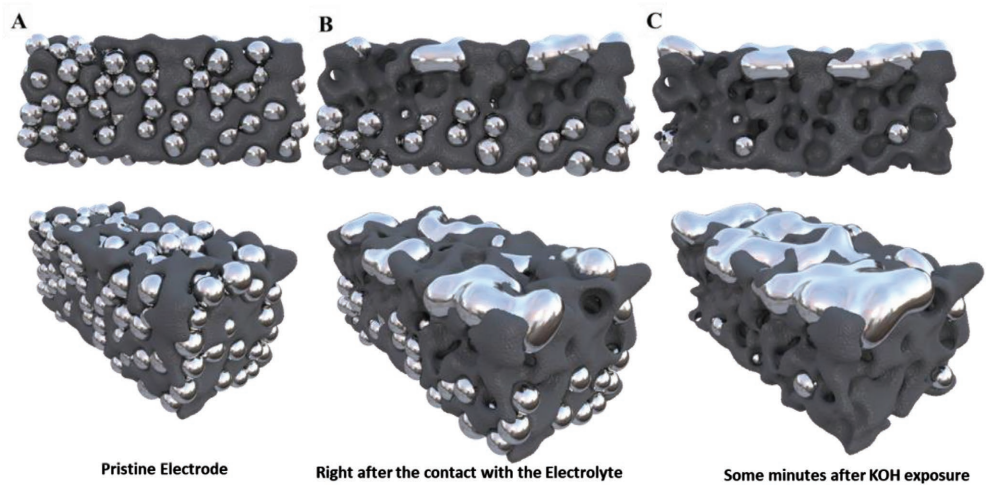
Suggested model for the Ga-C-SIS electrode. A) Before contacting the electrolyte. B) After contacting with the electrolyte, forming a liquid aggregated interface. C) After electrochemical cycling.
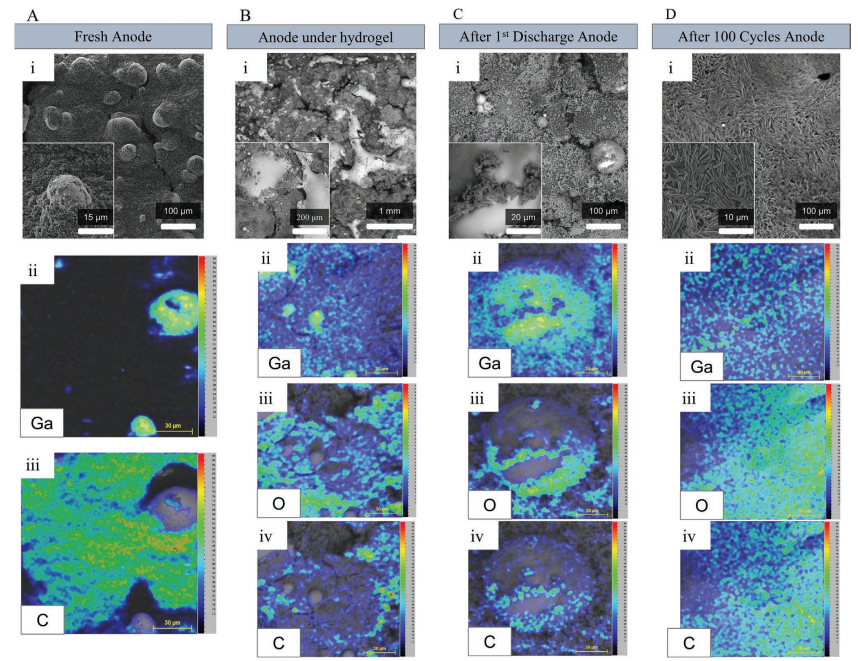
SEM and EDS of the Gallium-Carbon-SIS electrodes. A) Fresh electrode B) Electrode after being in contact with the electrolyte. C) After Discharging the battery D) After 100 charge and discharge cycles. In all images A, B, C, D: i) SE microscopy image; ii) color map of the gallium element intensity; iii) oxygen element intensity; iv) carbon element intensity
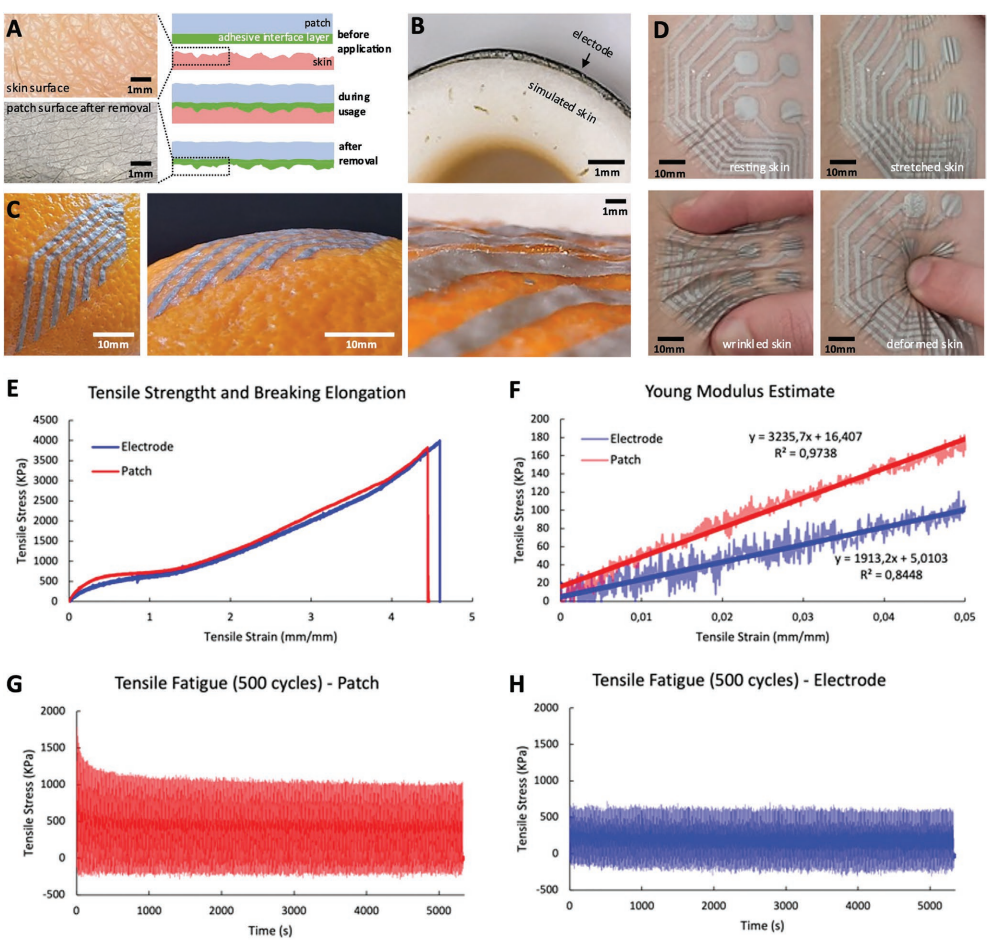
A) Skin wrinkles are imprinted on the adhesive interface layer of the patch. B) Cross-section image of a printed electrode conformed to a nonplanar skin replica. C) Images of a patch conformed to the rough surface of an orange peel. D) The dynamic conformal nature of the e-patch: it keeps its conformability to the skin even under deformation. E) Strain–Stress curves obtained from quasi-static tensile testing for electrode and patch stackups showing a rupture strain ≈450% for both cases. F) Young’s modulus for both multi-layer stackups obtained from linear regression. G) Fatigue testing of the 4-layer patch stack for 500 cycles at a strain of 30%. H) Fatigue testing of the 2-layer electrode stack for 500 cycles at a strain of 30%. In plots E–H, one sample per test was used.
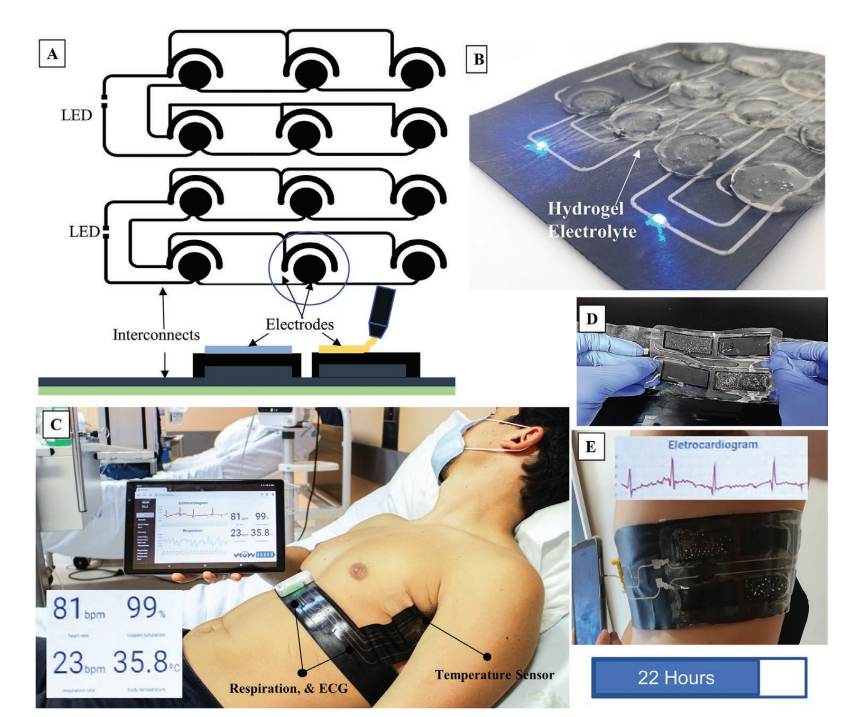
A) Schematic design of two multicell batteries connected in parallel and in series in a 3 × 2 arrangement. All of the layers where printed using the extrusion printer. B) Digitally printed silver gallium battery with the soft hydrogels lighting an LED. C) Biomonitoring wearable ”Wow Belt” acquiring body temperature, respiration and heart monitoring. D) Prototype of the printed battery used for the WoW belt before integration into the textile and. E) after integration into the belt, providing 22 h autonomy.