Anthropomorphic finger for grasping applications:
People involved:
- Mahmoud Tavakoli
- Andriy Sayuk
- João Lourenço
- Pedro Neto
Application of soft and compliant joints in grasping mechanisms received an increasing attention during recent years. This article suggests the design and development of a novel bio-inspired compliant finger which is composed of a 3D printed rigid endoskeleton covered by a soft matter. The overall integrated system resembles a biological structure in which a finger presents an anthropomorphic look. The mechanical properties of such structure are enhanced through optimization of the repetitive geometrical structures that constructs a flexure bearing as a joint for the fingers. The endoskeleton is formed by additive manufacturing of such geometries with rigid materials.
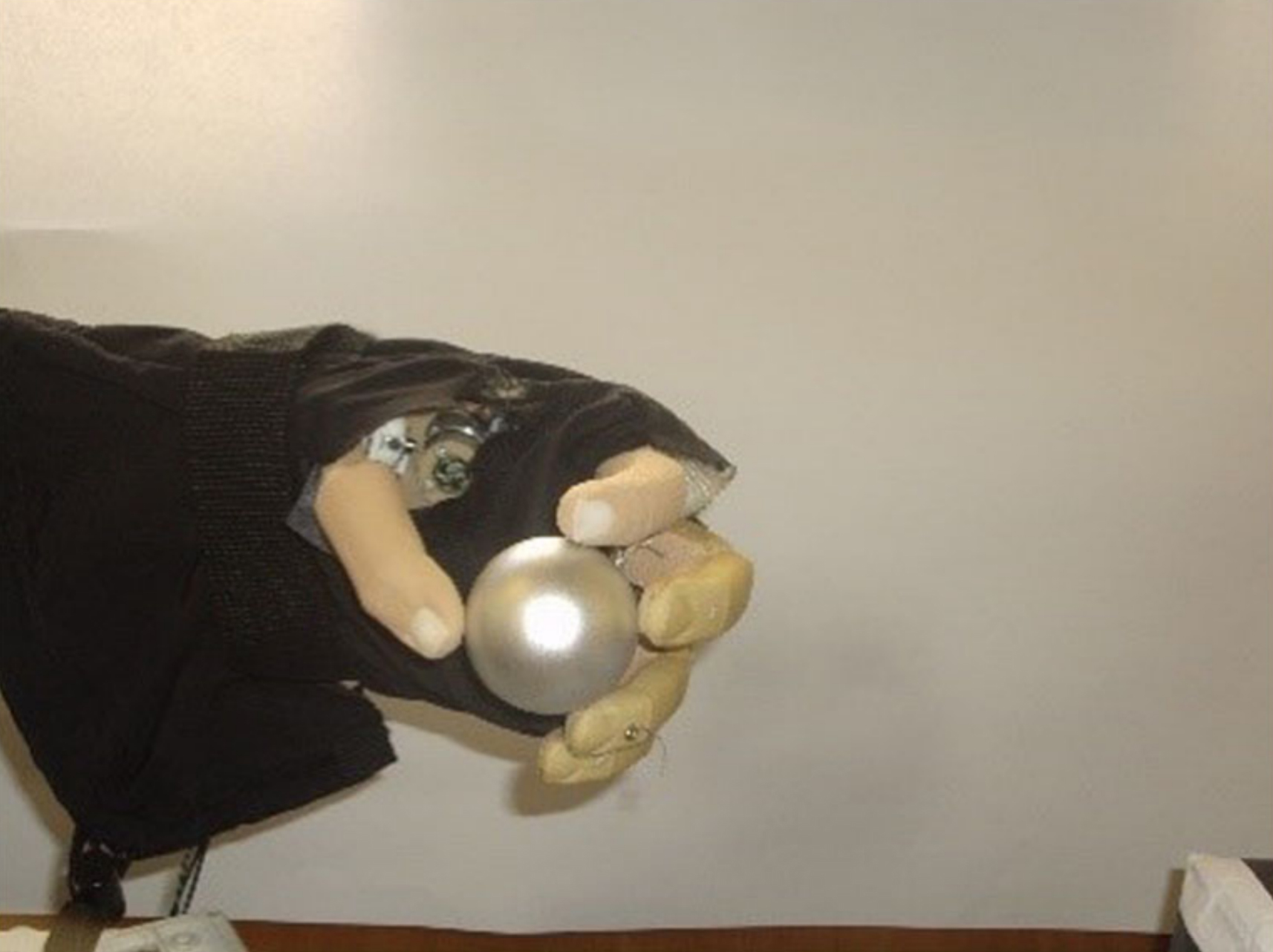
The ISR-Softhand grasping a spherical object. The exerted forces cause undesired deflections on the compliant joint of the thumb, affecting the grasp stability. Grasping heavier objects is impossible, even if the thumb can exert enough normal force.
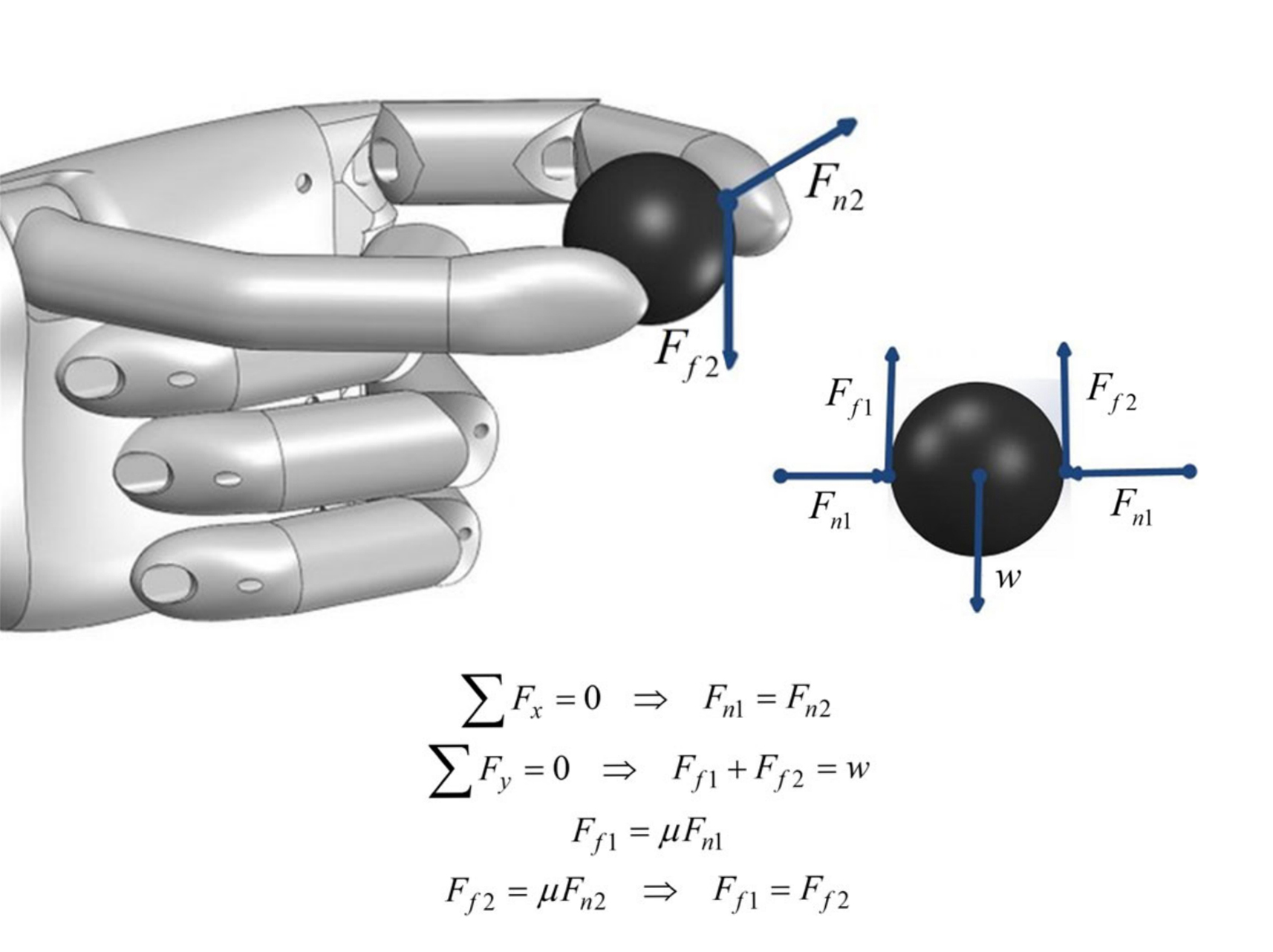
Forces applied to the fingers in a tip pinch.

A 3D printed endoskeleton integrating rigid joint reinforcements (a). The DIP joint is filled with some sponge and sealed with an elastic tube (b). This set is then placed in a mould (Fig. 6) which is formed from 3D scanning of a human finger and a resin is cast around the endoskeleton (c, d).
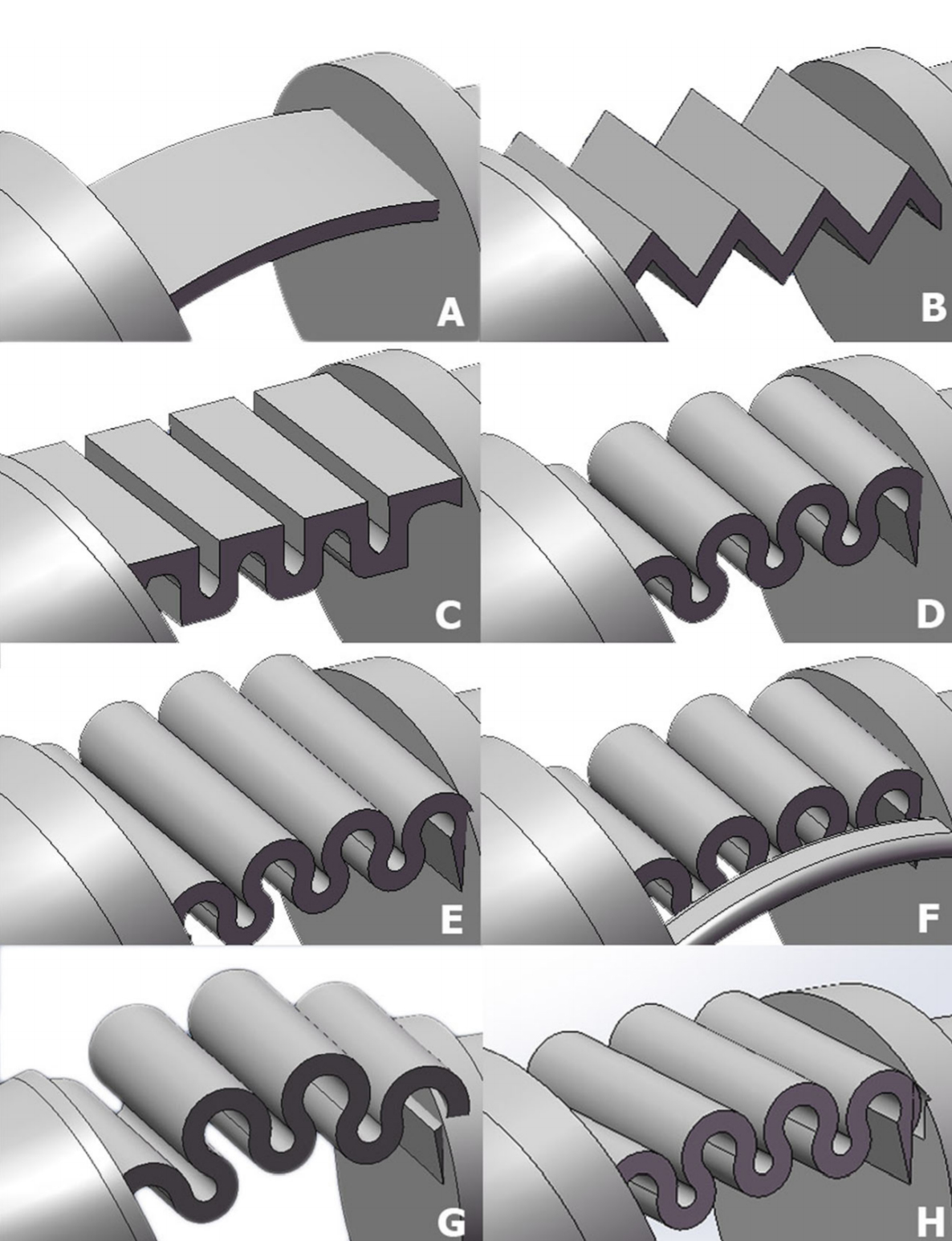
Different joint models used in tests.
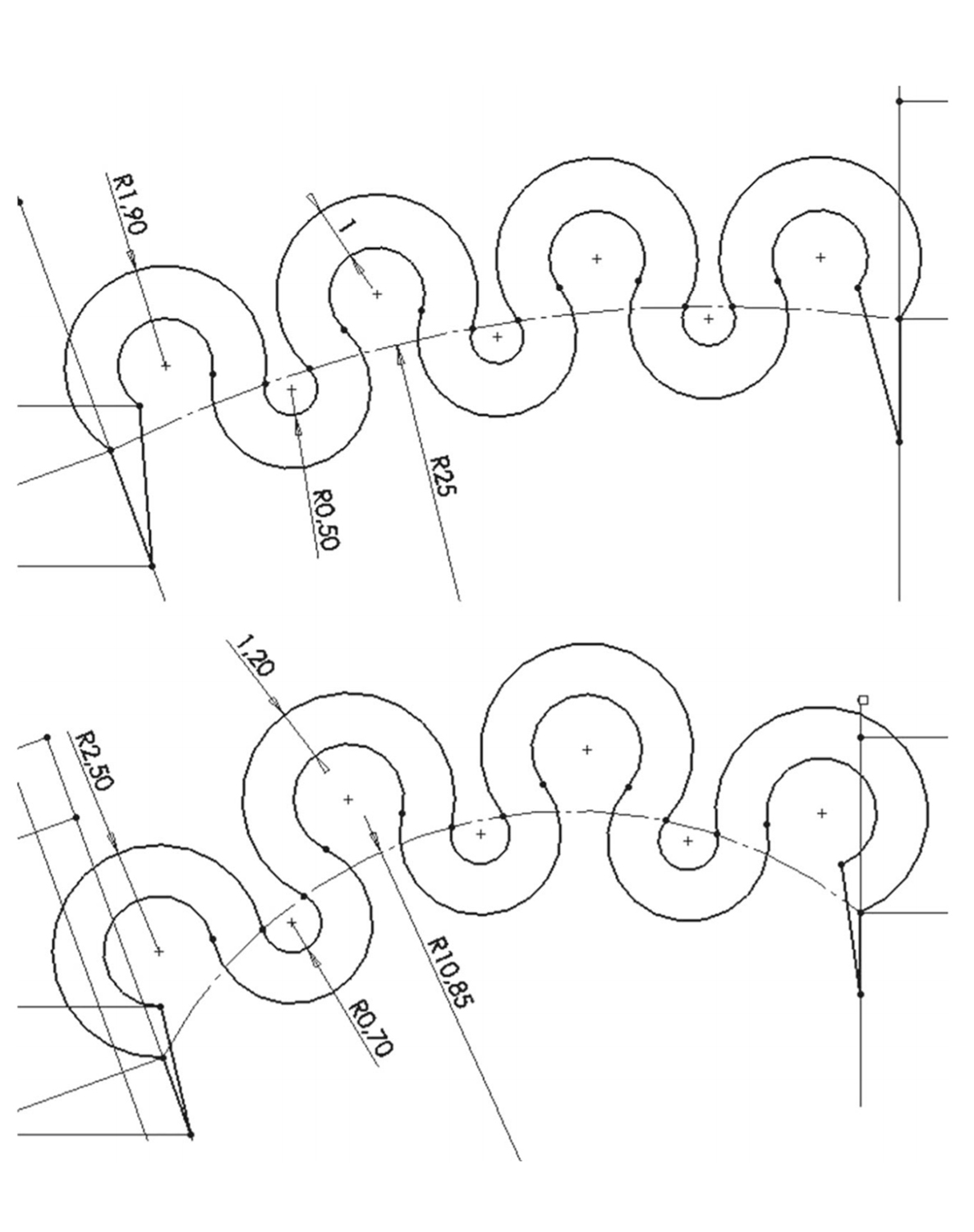
Geometry used in circular pattern for joint samples D, E and H (top), and for sample G (bottom).
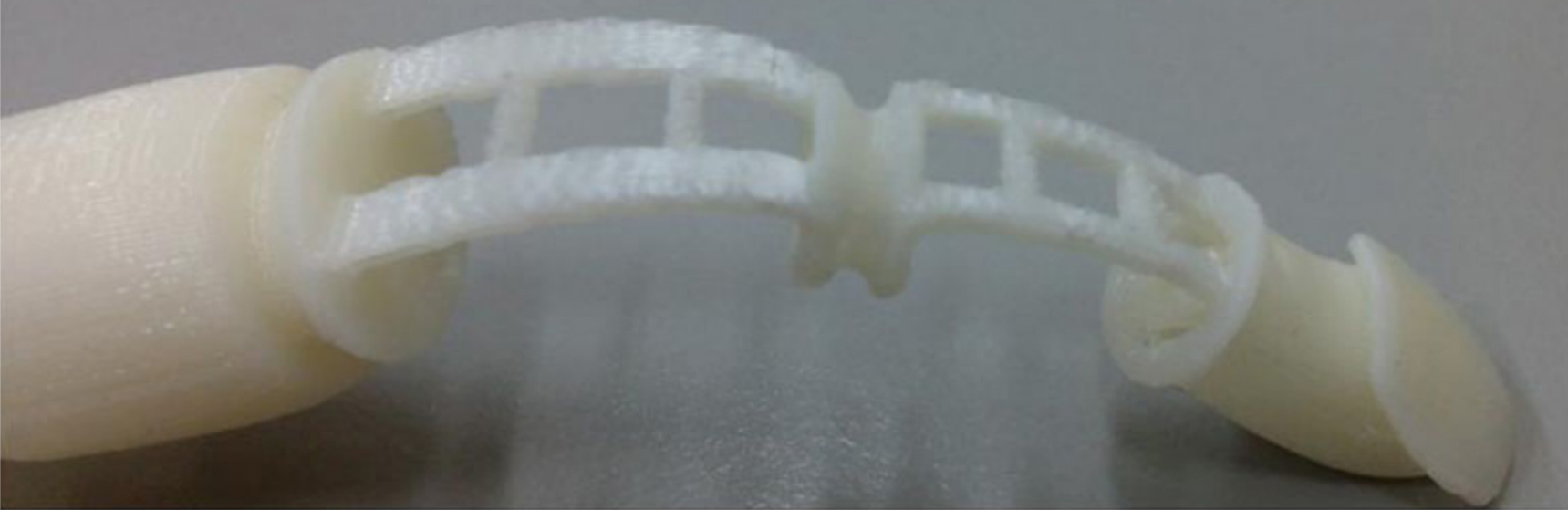
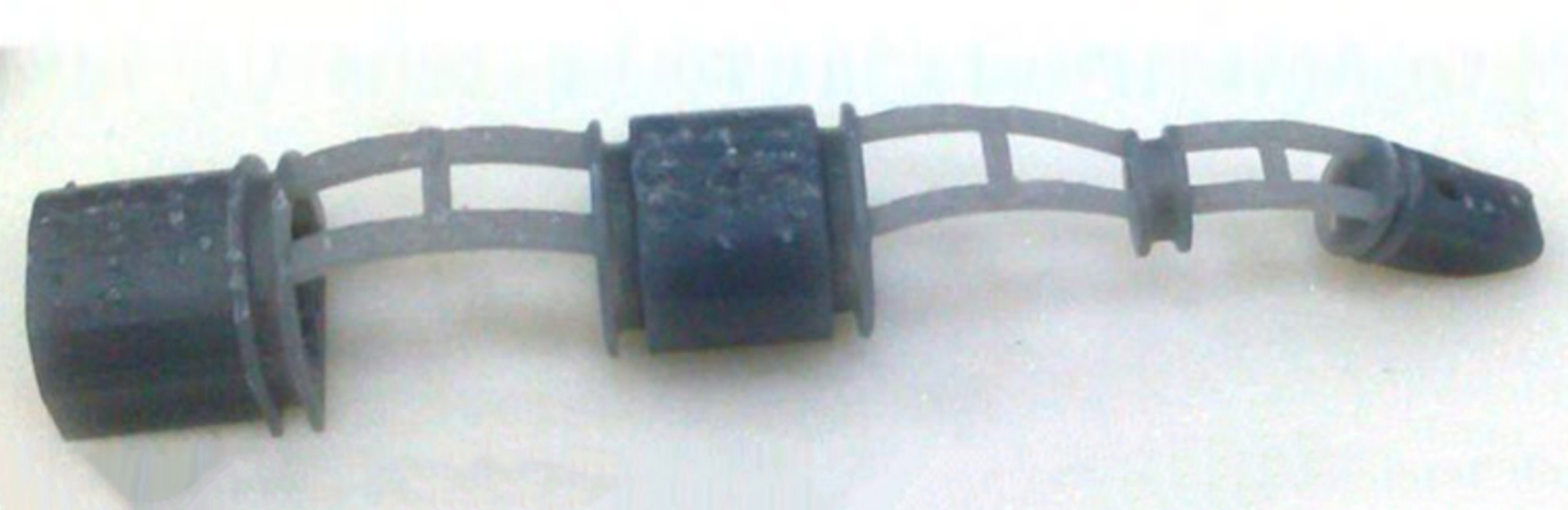
Finger printed with FDM method (top) and SLA method (bottom). In the FDM part, the visible defects on the joints reduce the actual yield strength of the joint. The SLA part do not presents the appropriate elastic properties.
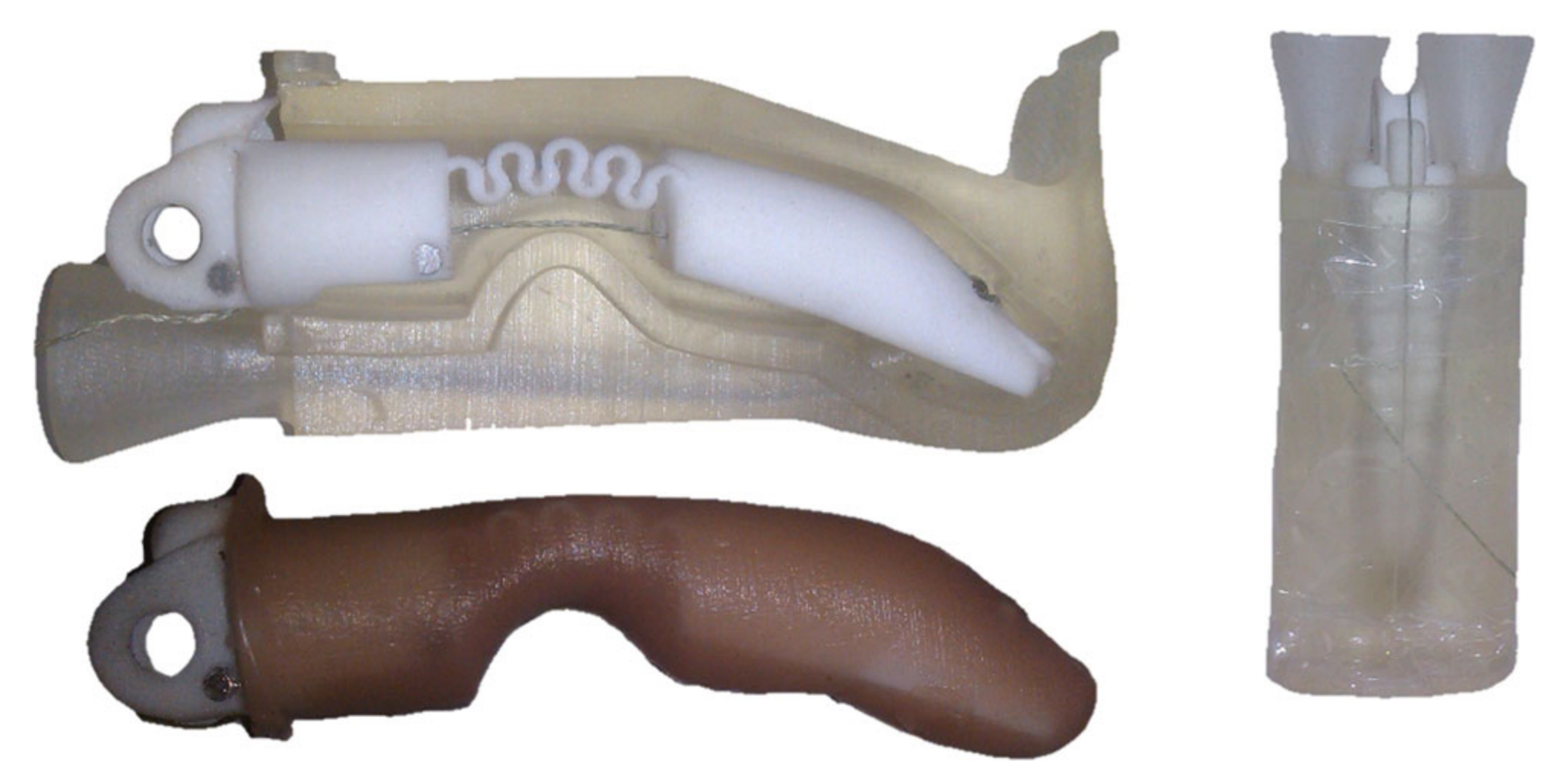
Fabrication process of the finger. The prepared 3D printed endoskeleton is placed into the mould and filled with silicone resin.
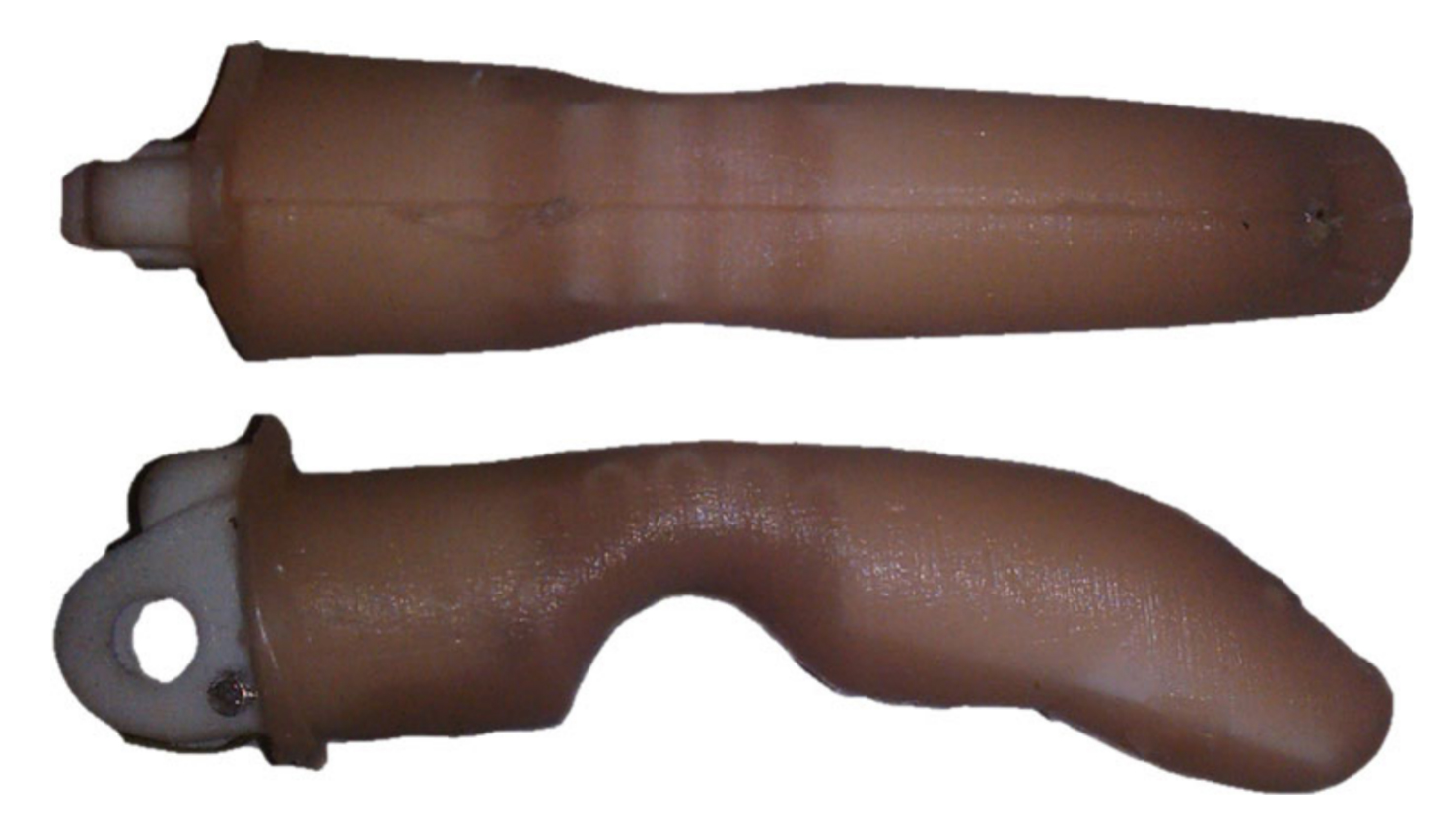
A sample prototype of the finger.
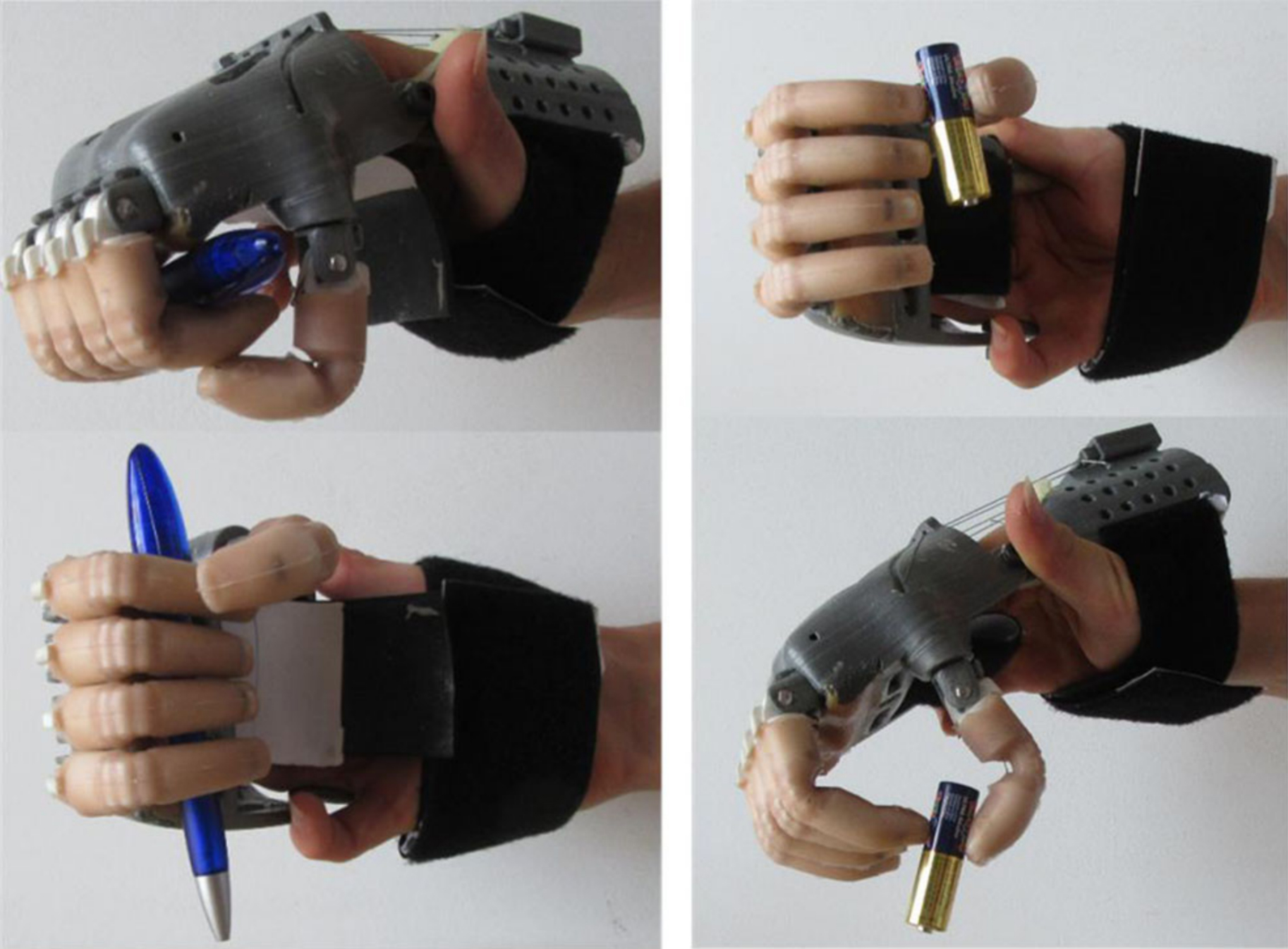
A prosthetic hand developed for an 8-year-old amputee using the fingers with the developed compliant joint. It is based on the Enable community designs (actuated by the wrist/elbow movement).
Anthropomorphic finger for grasping applications: 3D printed endoskeleton in a soft skin.
Tavakoli, M., Sayuk, A., Lourenço, J. et al. Int J Adv Manuf Technol (2017) 91: 2607. https://doi.org/10.1007/s00170-016-9971-8