A Compact Two-Phase Twisted String Actuation System:
People involved:
- Mahmoud Tavakoli
- Rafael Batista
- Pedro Neto
In this paper, we propose a compact twisted string actuation system that achieves a high contraction percentage (81%) on two phases: multi string twist and overtwist. This type of system can be used in many robotic applications, such as robotic hands and exoskeletons. The overtwist phase enables the development of more compact actuators based on the twisted string systems.
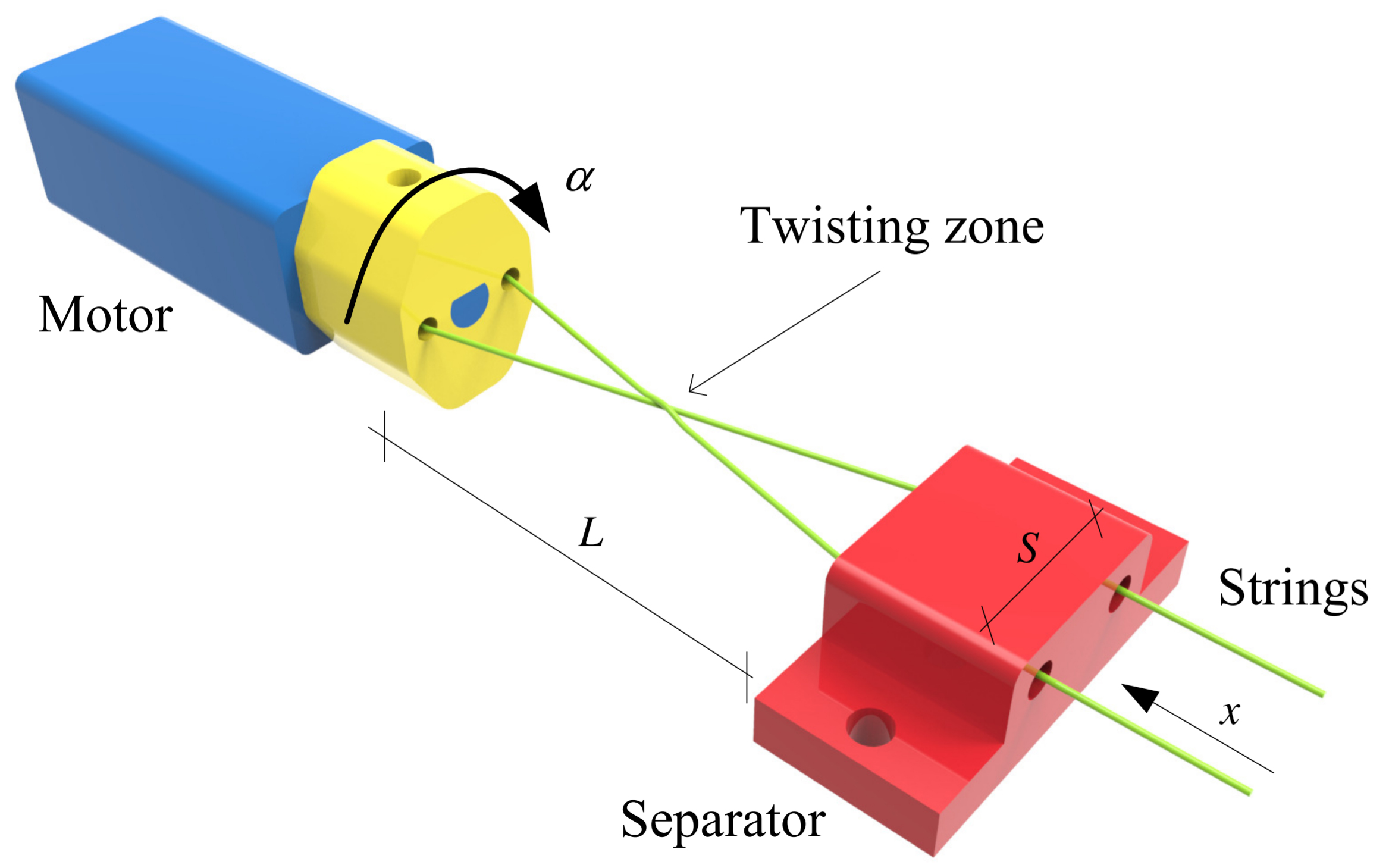
Twisted string system: electric motor, strings, connection between motor shaft and strings and separator. L is twisting zone length, α is the rotational angle of the motor shaft, x is the linear displacement of the strings and S is the distance between the holes of the separator.
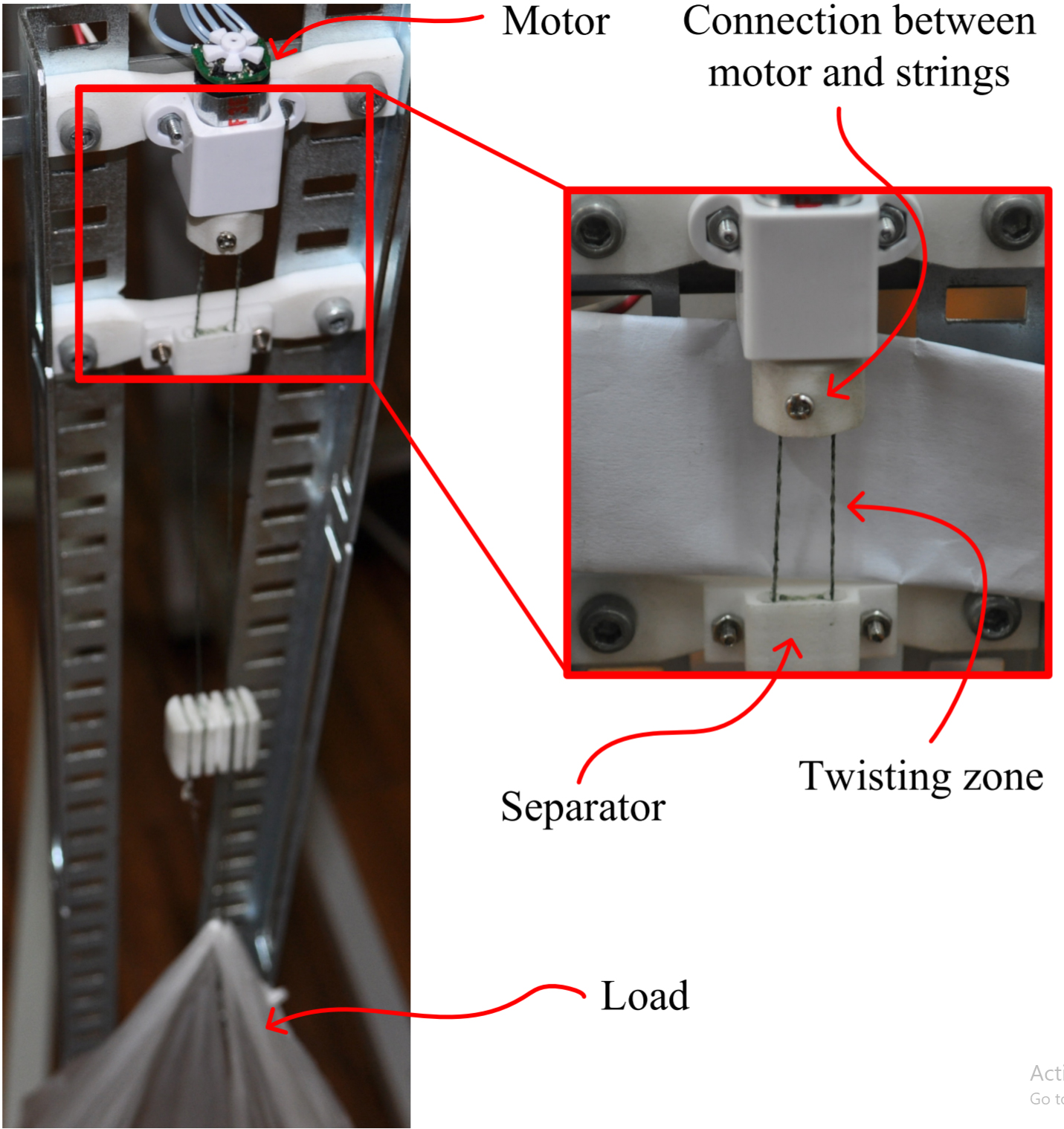
Twisted strings actuation system prototype that was used to lift a 2 kg weight.
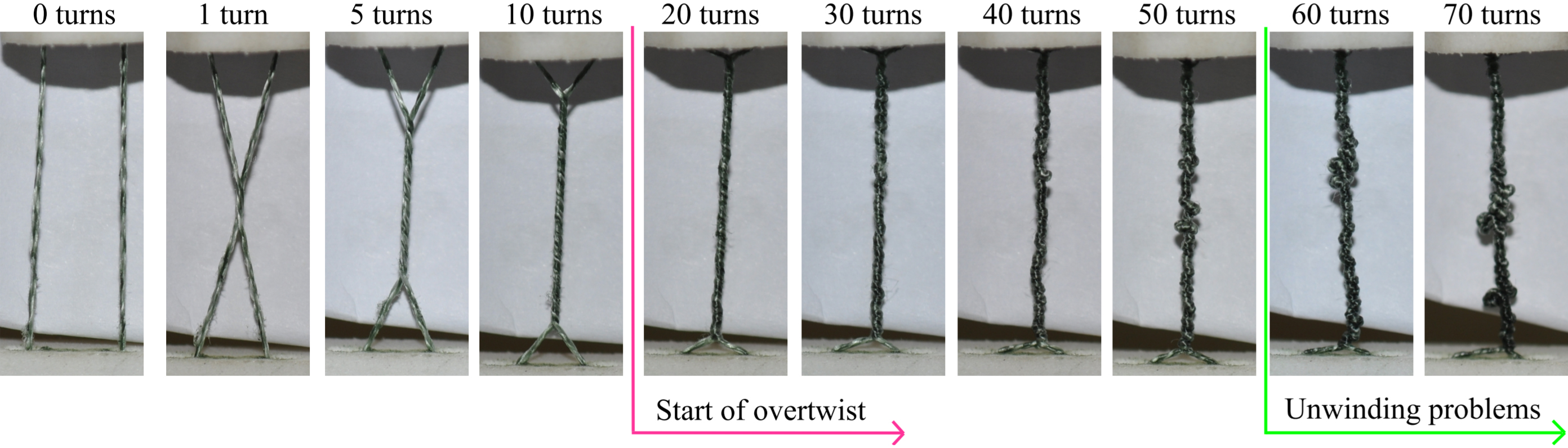
Snapshot of the twisted string system with 2 strings from 0 to 70 turns. As can be seen, overtwisting starts to happen after 20 turns. After 40 turns, overtwist is not evenly distributed over the twisting zone and local overtwist starts to happen, which can be seen in 50 turns snapshot.
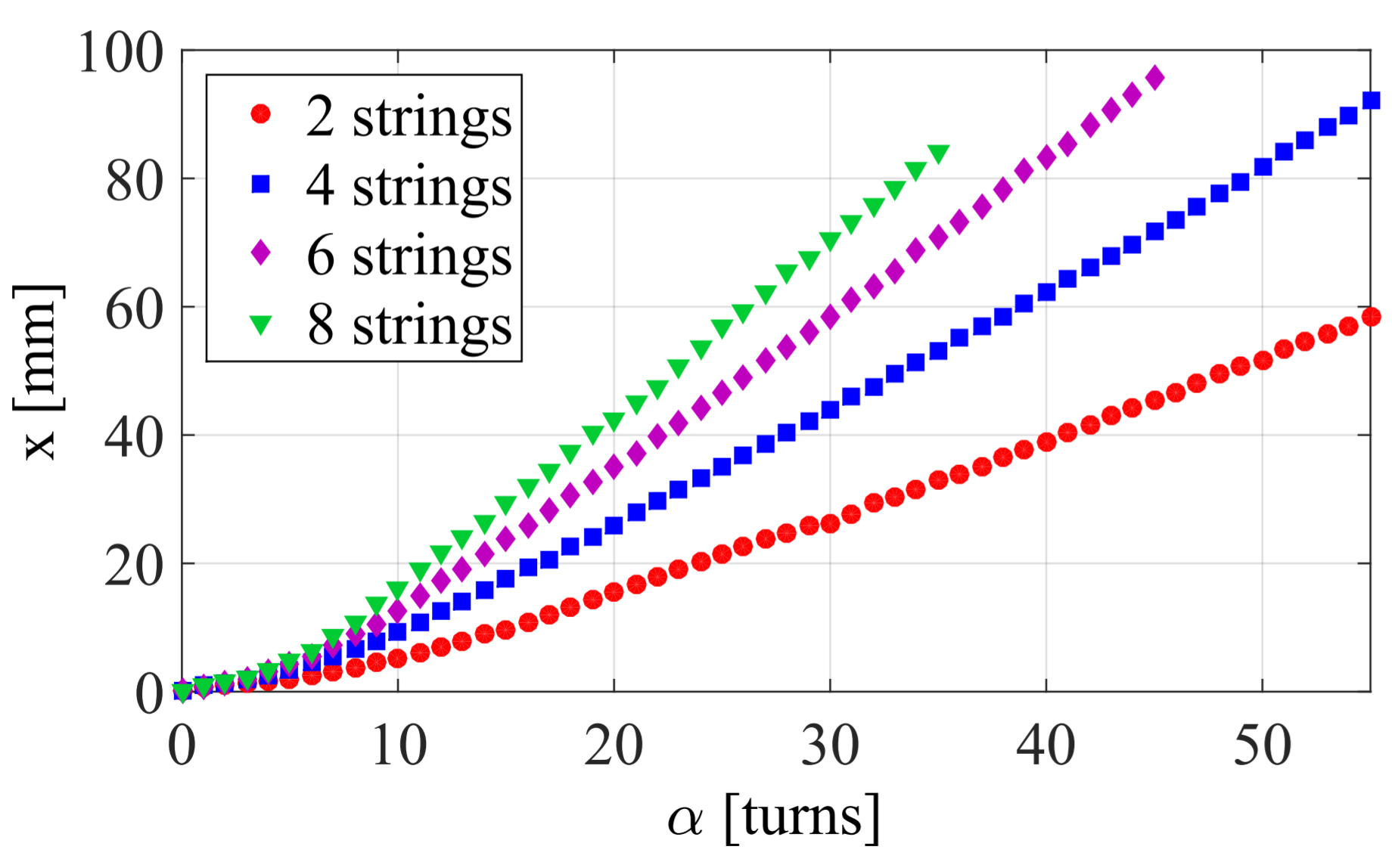
Experimental results for various number of strings in the system, with x being the linear displacement and α the number of turns at the output shaft of the gearmotor.
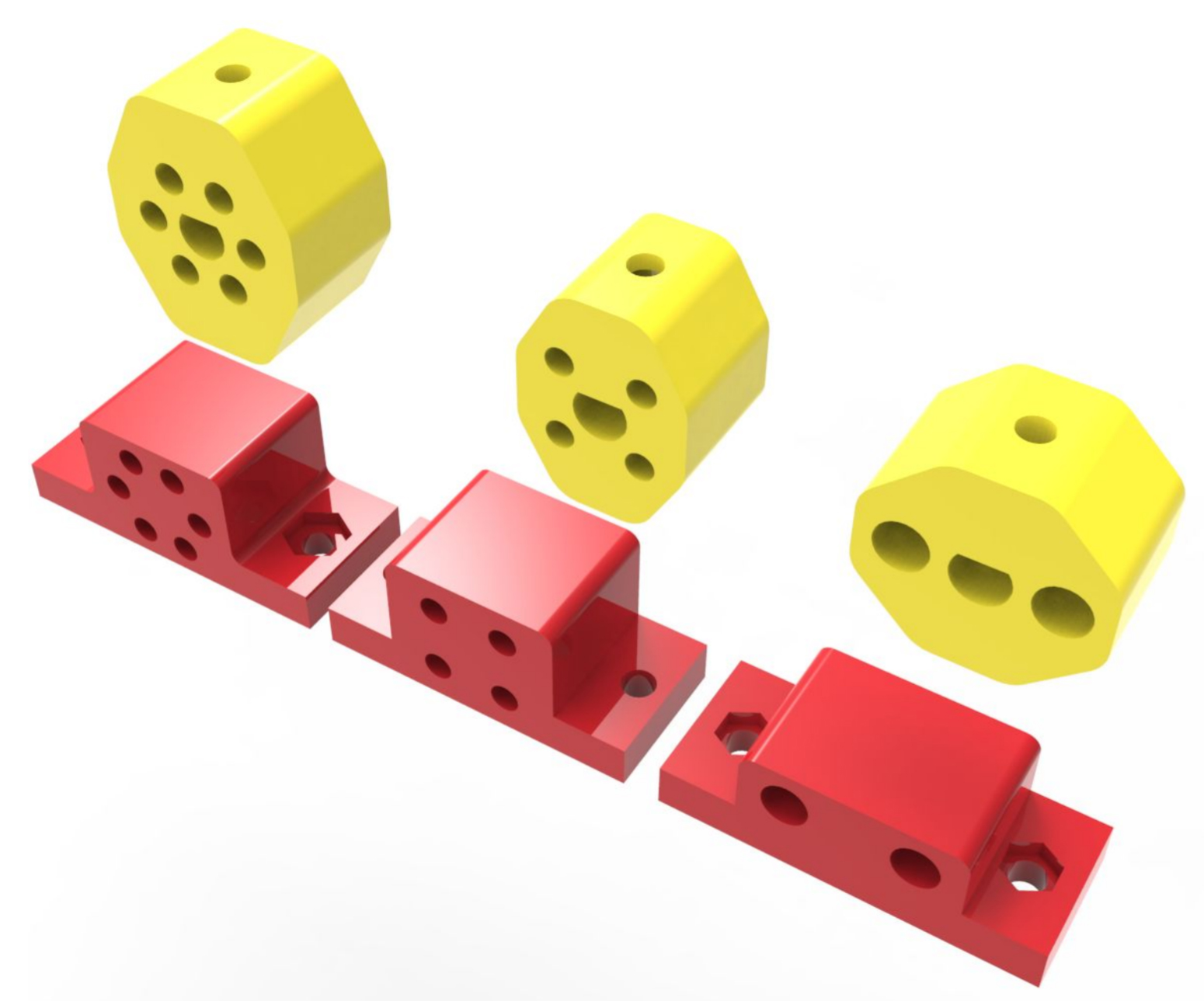
The different separators and motor shaft connectors tested. The distance between the holes of the separator, S, remains the same in all of them.

Zoom of strings under twisting close to the separator. The red rectangle highlights the zone where the strings twist when they come out of the separator. In that zone the string bundle diameter remains constant for the entire range of overtwisting.